CNC Rotary Table Shot Blasting Machines

Reduced Setup Times
Motion control reduces costly nozzle setup time, and time cycles.

Precise Control
CNC motion allows a nozzle to follow the contour of a part for consistent and true intensity and coverage throughout the part.

Flexibility
Rotary table machines offer customers repeatable and stable systems for a wide variety of parts.
Exact, repeatable control.

Robust Customization
CNC rotary table shot blasting machines can be built to fit parts of any size and weight, and are available with multiple options such as:
- Multiple shot delivery systems including continuous direct pressure, gravity feed suction, or dual shot delivery.
- Up to six axis of motion depending on the application
- AMS2430 compliant
- Propietary CIMCAP CNC software
- Fanuc CNC controllers
- Single or batch processing
- Robotic articulating arm loading integration
- Assembly line integration
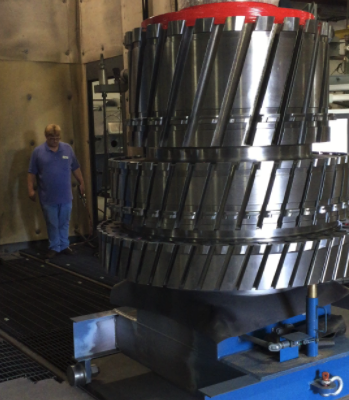
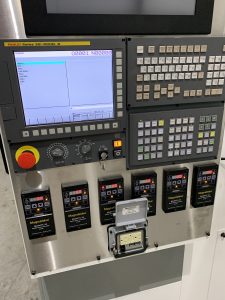
Ease of Use
Controlled Intelligent Motion Computer Alarm Parameters (CIMCAP) is available as an option on all of our CNC equipment. Our PC‐based passive computer program allows a novice to learn how to quickly program the CNC system.
A simple click on a specific CIMCAP icon and the program will write the G code line for the programmer. CIMCAP is also used for process monitoring and alarm management.
Advanced Motion Control
Using motion control allows the user to reduce the costly nozzle setup time. It also allows for total coverage of the parts while using less compressed air. Time cycles are typically much reduced because no unwanted over peening/blasting is done.
Controllers are off-the-shelf and use industry-wide G code commands. The controller’s service life is measured in decades.
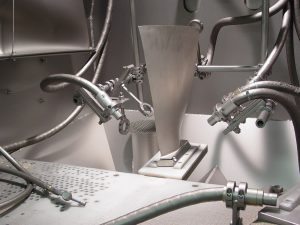
Robotic Arm Shot Peening
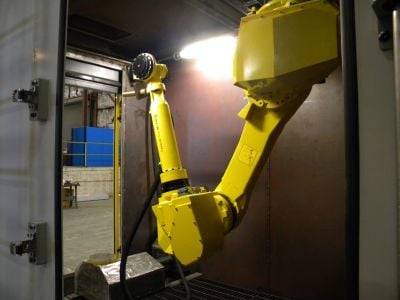
Articulating arm robotics can be added to the interior or exterior of all IPS machines. Normally this type of robotic motion is specific to an application, such as plastic media blasting, or a specific motion that a CNC-gantry robot cannot provide. Articulating arm robots are historically cheaper than CNC-gantry robots, but can be more expensive to repair should wear occur inside the enclosure. Articulating arm robots also require larger enclosure sizes to accommodate the robot motion. The main benefit of an articulating arm robot motion is speed and reach. Systems can also be integrated with other loading robots and multi systems tasking.
Robotic articulating arm machines offer users a fast nozzle motion for larger parts that need quick cycle timers. Customers may choose the robot of choice. Another benefit to some customers is the familiarity of robot programming. Machine enclosures are custom built to allow the robotic arm to fully move to peen or blast the users part.
Additional Features
Rotary Table
Direct pressure or gravity feed suction delivery
AMS 2430 and AMS 2432 compliant
Single or batch processing
Easy-to-use Cimcap software
Cabinet size and weight requirements can fit any part
Robotic loading integration
Integrated loading crane